Plasma cleaning
for oxygen and PWIS / LABS free applications
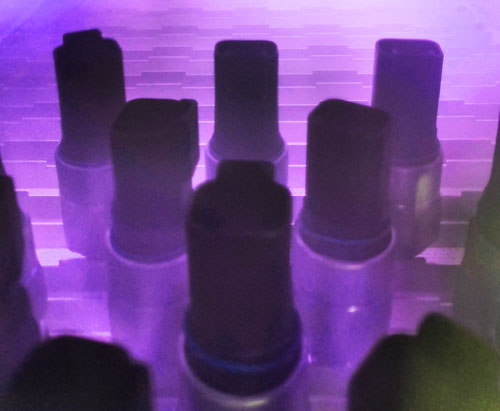
We offer our customers plasma-cleaned pressure switches and transmitters for various industrial and medical applications. The plasma cleaning process is subject of our internal quality management process according to DIN ISO 9001:2015. The high level of purity (max. 20 mg/m² organic residues) is regularly verified by a national accreditation body (DAkkS).
When handling oxygen, the country-specific safety and accident prevention regulations must be observed. For oxygen applications, we recommend using exclusively plasma-cleaned pressure switches and transmitters with EPDM sealing.
The requirements for components free of paint impairment substances (PWIS/LABS) have also increased in recent years. By extending the plasma cleaning process and using silicone-free gloves and PE bags, we are able to offer PWIS/LABS compliant pressure switches and transmitters for the OEMs and paint shops.
Levels of purity
- Free of oil and grease ▪ individual parts free of oil and grease
- Plasma cleaned (for oxygen) ▪ free of hydrocarbonbased substances
- Plasma cleaned (PWIS free) ▪ free of paint-wetting impairment substances (PWIS)
▪ assembly and adjustment free of oil and grease
▪ individually packed in PE bags
▪ individually packed in silicone-free PE bags
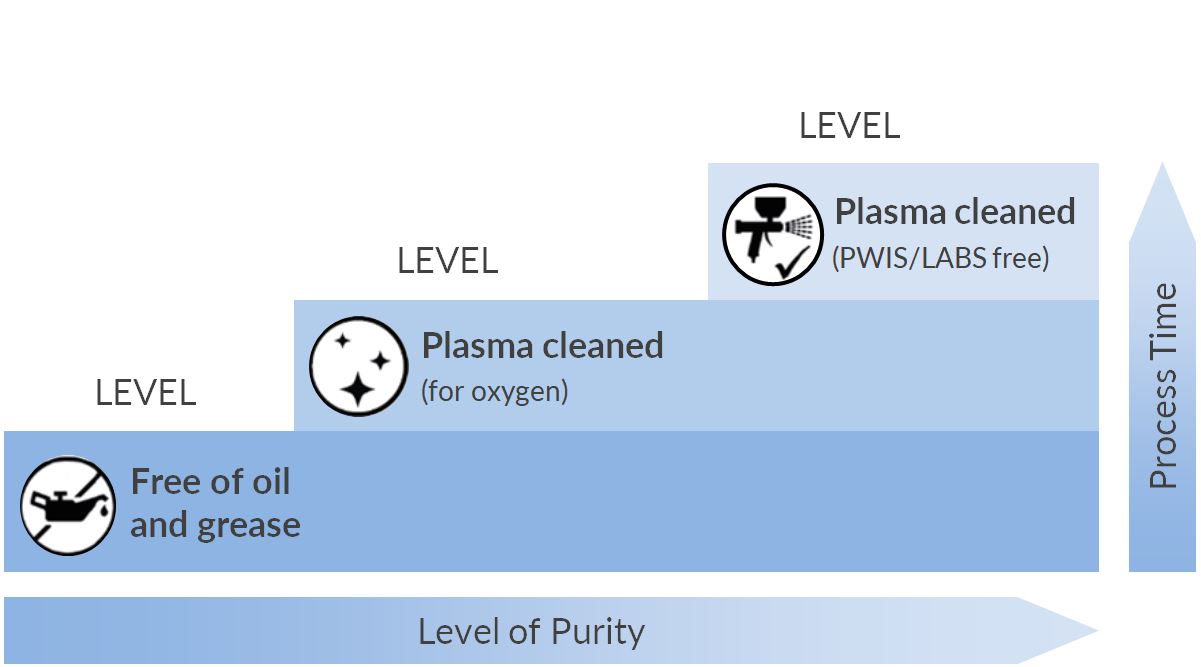
Application areas
At a glance

Purity
Maximum quantity of hydrocarbon-based compounds is 20 mg/m2 (according to ASTM G93:2019)
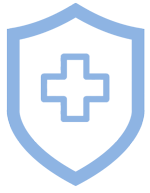
Safety
Approved burnout resistance of EPDM sealings by the Federal Institute for Materials Research and Testing (BAM)
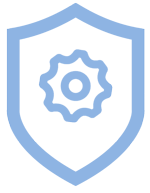
Efficiency
Regular verification and approval by a national accreditation body (DAkkS).
FAQs
- Plasma (Greek: the formed) is a reactive gas consisting of free, energy-rich electrons, ions and neutral particles
- The proportion of charged particles can vary between 1 % and 100 % (full ionization) and determines the electrical conductivity of the plasma
- Since plasma can be generated from the gaseous state by supplying energy, it is also referred to as the fourth state of matter in addition to solid, liquid and gaseous.
When handling certain media, certain safety regulations or industrial requirements must be observed:
- Oxygen applications
Oxygen (O2) itself is not combustible. However, in conjunction with a combustible substance such as oil or grease, spontaneous ignition may occur due to frictional heat, electrostatic discharge or sparking. Even a slight increase in the oxygen content can accelerate the combustion process considerably - PWIS/LABS compliant applications
PWIS/LABS are paint wetting impairment substances such as lubricants, oils, greases or silicones. During the painting process, PWIS/LABS contamination can cause partial coating defects - so-called craters - as well as large-area disturbances of the wetting film, thus impairing the quality and durability of the paint.
For both applications (oxygen and LABS compliance) we recommend the exclusive use of plasma-cleaned pressure switches and transmitters with EPDM sealings.
- Residue-free surface cleaning
Plasma cleaning reliably removes any organic hydrocarbon-based (CH chains) contamination from surfaces.
In addition to oils and greases, these include lubricants, silicones and other substances that interfere with paint wetting (PWIS/LABS).
The plasma cleaning process enables a maximum level of purity of 20 mg/m² (stage B) in accordance with ASTM G93:2019. - Surface activation
Through plasma cleaning, a temporary increase in surface energy can be achieved. By plasma activation, the surface of the pressure switches and transmitters is changed, which increases the wetting ability. - Further advantages
Compared to water-based cleaning processes and solutions, plasma cleaning is efficient (low energy and process costs) and environment-friendly.
In addition to that, sensitive surfaces, such as polymers, are not damaged and an immediate processing is possible.
The operating principle of a plasma cleaning system can be divided into four steps:
1. Evacuation of process chamber
Pressure switches and transmitters of different sizes can be placed inside the process chamber.
The process chamber is hermetically sealed and evacuated by means of a vacuum pump.
2. Oxygen enrichment
Pure oxygen (O2) is supplied as process gas at approx. 1 mbar. A high-frequency generator forms an electromagnetic field as energy source.
The oxygen molecules are ionized and transferred into the highly reactive plasma. The remaining nitrogen begins to glow violet during reduction.
3. Plasma cleaning
Organic contaminants based on hydrocarbons (CH chains) are completely decomposed in the plasma.
During the plasma cleaning process, oxygen is continuously supplied and used gas (decomposition product of the hydrocarbons) removed by the vacuum pump.
4. Venting of process chamber
After the treatment is completed, the process chamber is ventilated and the plasma-cleaned products are handled with gloves.
In a further step the pressure switches and transmitters are individually packed and sealed in PE bags.
Special Markings on the bags inform the customer about the respective cleaning process.
- Individual parts free of oil and grease
When selecting our suppliers, we pay attention to the provision of oil- and grease-free individual parts within the scope of quality assurance. - Assembly and adjustment free of oil and grease
Trained personnel and strict operating regulations ensure that our products are assembled and adjusted free of oil and grease.
It cannot be ruled out that, due to the production process, small quantities of lubricating oil or skin grease may occasionally stick to a workpiece.
We therefore recommend to use exclusively plasma-cleaned pressure switches and transmitters with EPDM sealings when handling oxygen or other flammable air-gas mixtures.
- Plasma cleaning
During plasma cleaning, the pressure switches and/or transmitters are freed from organic contamination based on hydrocarbons.
A maximum of 20 mg hydrocarbon compounds per m² can be detected. This corresponds to stage B (< 33 mg/m²) according to ASTM G93:2019.
To avoid subsequent contamination, the products are removed with gloves and individually packed and sealed in PE bags. - Oxygen applications
The burnout resistance of our EPDM sealings has been certified by the Federal Institute for Materials Research and Testing (BAM). Therefore we exclusively recommend the use of EPDM sealings for oxygen applications.
The maximum permissible pressure for oxygen applications varies depending on the housing material from 10 bar (galvanized steel), 35 bar (brass) up to 250 bar (stainless steel).
- PWIS/LABS
The acronym PWIS refers to "paint wetting impairment substances" such as lubricants, oils, greases or silicones. Even in small quantities, PWIS/LABS contaminations can cause partial coating defects (craters) as well as large-area wetting disturbances of the paint film.
Industrial painting processes of vehicle and engine manufacturers (OEMs) are often subject to strict requirements regarding the LABS conformity of individual parts. - PWIS/LABS compliance
Due to a longer duration of the plasma cleaning process and the use of PWIS/LABS free gloves and PE bags, our pressure switches and transmitters achieve PWIS/LABS conformity according to the national standard sheet VDMA 24364.
As verification, we gladly issue a manufacturer's declaration "Plasma cleaned for PWIS/LABS free applications".
Plasma-cleaned pressure monitoring products are used in numerous applications, e.g:
Medical technology
- Ventilation and anaesthesia equipment: Medical oxygen for ventilation in emergency medicine and the oxygen treatment of chronic lung diseases (COPDs)
- Laboratory autoclaves and steam sterilizers: Thermal treatment of materials in the overpressure range up to a certain degree of purity (ISO 8573-1)
Production and manufacturing
- Autogenous welding and flame cutting: Outflowing fuel gas-oxygen mixture is ignited and oxidizes in a kerf on the workpiece.
- Glass and steel industry: Pure oxygen is added to the glass / blast furnace to accelerate and optimize the melting process (Oxyfuel process)
- Textile industry: Highly dosed oxygen is used as a bleaching agent for fibres and cellulose
- Varnishing industry: Use of PWIS/LABS compliant products within the PWIS/LABS zones to prevent contamination.
Chemical, pharmaceutical and food industry
- Chemical industry: Process engineering oxidation of organic compounds
- Pharmaceuticals: Distillation and oxidation of sterile water
- Food packaging: Fumigation of food under modified atmosphere (liquid oxygen)
Water treatment
- Drinking water treatment: Removal of iron, manganese, ammonium, hydrogen sulphide or methane in drinking water by adding oxygen.
- Wastewater treatment: Ozone (O3) for oxidation of pollutants and persistent substances in wastewater treatment plants
- Ozone production: disinfection of swimming pools and process water
- Over the last decades, we've gained an extensive know-how and experience in the field of pneumatics, hydraulics and fluid technology.
- We are experts when dealing with demanding and safety-relevant applications with or without inflammable media (ATEX / IECEx).
- Our technical customer service and international sales partners are always happy to consult you.